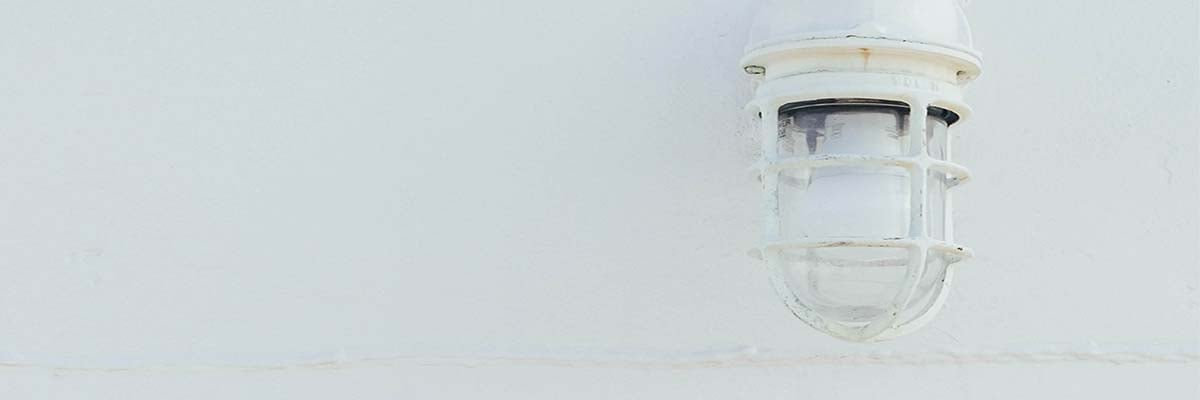
The daily grind – Cat fines and engine wear, Part 2
In Part 1 of our cat fines discussion we described the nature of the cat fines problem and the growing threat it will pose in the coming low-sulphur era. Now we turn our attention to how owners and operators will need to combine established technologies with updated knowledge and practices to ensure the safety of their ships.
Separation basics
At bunkering, fuel is pumped into a ship’s storage tank, and from there transferred into the settling tanks (enough to support 24-48 hours of operation at a time). Small quantities of some larger cat fines will settle under gravity in the tanks, but not enough to protect the engine – and rough seas can send contaminants back up through the fuel.
From the settling tank, fuel is then passed through a separator. Separators – also known as purifiers –spin the cat fines, water, and other contaminants out of the fuel, which then flows to a service tank before being conditioned and pumped into the engine. Separators may be configured individually or in parallel, and it’s critical to match the size of the separators to the needs of the engines they serve.
The density, viscosity, feed flow rate, and temperature of the fuel are all critical factors in determining the effectiveness of the separator. As the available choice of fuels changes in the low-sulphur era, crews will need to maintain a much higher level of understanding than they have been able to get away with up to now.
Going with the flow
The rate at which fuel flows through a separator is closely linked to the efficiency of the separation. Put simply, decreasing the flow, increases the efficiency, allowing the centrifuge more opportunity to remove particles.
Traditionally, separator flow was set at 100 percent of the engine’s maximum fuel consumption, plus an added safety margin. But ships rarely run at 100 percent capacity, especially as slow steaming becomes more common. Therefore, as described in CIMAC paper 51 on on-board fuel cleaning, “there is a large potential for increasing the separation efficiency by applying automatic flow control in relation to the actual fuel consumption”. In fact, not only does flow control increase separator efficiency, it also improves fuel economy.
Known unknowns
Complicating fuel separation in the low-sulphur era will be the as-yet-unknown qualities of the new fuels that will enter the market, and the blending of fuels.
It is certain that cat fines will be present in new fuel blends produced post 2020 (including renewable fuels), and operators will need to be diligent in testing to know what they are dealing with. Beyond contamination, the stability and potential incompatibility of new fuels will need to be closely monitored to prevent sludge from forming, which can create many problems in the engine room, including reduced separation efficiency.
The need for expertise
What this all adds up to is a greater need than ever before for knowledge and expertise in fuel treatment. And this need applies to the design of the engine room, the training of the crews, and the quality of service support.
Designing and building
At the design stage, ship owners and operators need to think beyond commodity solutions for high cat-fine conditions. Ship designers should consider the separators not as standalone units but as part of system, complemented by properly configured settling tanks, flow control mechanisms, thermal controls, and more. A systems approach means not leaving crucial engine protection decisions up to the shipyard, but instead taking the lead in specifying the full fuel line.
Crewing and training
Both at bunker and at sea, tomorrow’s crews will need the skills and understanding to handle a great range of variables. However, a recent Lloyd’s List Business Briefing highlighted that the industry faces a shortage of skilled crews worldwide. As Iain White, global marketing manager, Fuels and Lubricants for ExxonMobil explained: “We run a number of technical programs helping ship owners manage their engines and their equipment and increasingly we find that the engineering crews on the ship don’t understand how to run the equipment that they’ve already got.”
“Training is very much part of your risk management strategy,” said White. “You’ve already paid for the kit; you might as well learn how to use it right.”
Testing, monitoring, and servicing
No matter how good the design and build of a system, regular and responsive maintenance is a must. To start with, crews will increasingly rely on testing – both in labs, and to the extent possible, on board – to understand the characteristics and needs of their new fuels.
In operation, because of the wider variety of fuels, and the greater risk of contamination, more careful monitoring will be necessary.
Regular cleaning of tanks and separators is vital, as rough seas can stir up settled cat fine sludge and overwhelm the separators.
In addition to spotting problems with the fuel itself, crews will need to be alert to the warning signs of damage to equipment and machinery. In the case of cat fines (and other problems), some of the key indicators that serious damage is already occurring are lower pressure, sump contamination, and drops in engine efficiency. Immediate response to these signs can help mitigate further damage and costs.
Equipment that is easily serviced on board by crews helps ensure swift reaction, but when problems exceed the crews’ expertise, it’s essential to have rapid access to skilled, knowledgeable service technicians anywhere in the world.
Where to now?
As we sail into low-sulphur era, the risks of high-cat-fine fuels present a challenge for the industry as a whole. Much good work is already being done to raise awareness, such as the CIMAC-51 paper noted above, and the Cat Fines – Guidance Notes of Lloyd’s Joint Hull Committee, not to mention regular reports in industry news sources.
We really are all in the same boat on this issue, so continuing an active and open dialogue on cat fines can only benefit the entire global fleet.
Refuel your knowledge
Download the Alfa Laval Adaptive Fuel Line Blue Book
Будь ласка, зв’яжіться з нами для отримання відповідей на запитання і заявок на обслуговування.
З питань морського обслуговування, будь ласка, телефонуйте
+46 4636 7700
або надішліть електронне повідомлення на адресу
marine.service@alfalaval.com